新聞中心
前方高能!鋁合金壓鑄生產中金屬損耗的計算及管理干貨大全
作者: 秦皇島六合科技開發有限公司發布時間:2021-12-31 13:50:06點擊:627
鋁合金是壓鑄生產中最大的單一消耗物質,在鋁合金熔煉過程中,總會因氧化和操作等許多因素,造成相當大的鋁材損耗,它不僅白白損失了大量的鋁材,且造成許多能源損耗,加上大量熔煉氧化物的產生也會影響鋁液的質量,給產品帶來各種不利的結果,有效地控制金屬的流失可以在較大程度上增加企業的贏利。相反,在生產中不良的控制措施會造成過多的材料損失,造成生產成本的直接上升。
壓鑄過程中鋁合金材料損耗有以下幾方面:
1.熔煉中的燒損及揮發;
2.除渣時帶出;
3.壓鑄件飛邊毛刺;
4.澆口、料餅、廢鑄件等重熔的燒損及揮發;
5.因機床、模具等原因,造成壓鑄件重量增加。
一
在溶化金屬過程中的金屬損耗
(一)損耗原因及去向
在鋁合金熔煉過程中,由于鋁氧化以及鋁與爐壁、精煉劑相互作用而造成不可回收的金屬損失叫燒損。燒損和渣中所含的金屬總稱為熔損。只要是大氣條件下作鋁的熔煉,無論是純鋁還是合金,其中的各種元素都要經過高溫條件下的氧化作用,形成各種金屬氧化物,造成鋁液的損耗,自然也就按合金中不同的成分而生成各種不同的氧化物,從而使鋁材受到損耗,熔化完成后的鋁液,還需經過精練,精煉中添加的熔劑又因高溫分解發熱,進一步促使鋁液中各元素的氧化燒損。更使人注目的是,精練完成后,有許多完好的鋁滴,因界面張力的作用被粘附在渣中,成為渣鋁混合物,一起被當作渣扒出爐外。盡管這種混合物還可用很多方法來進行分離回收,但畢竟又需消耗許多能源,且回收過程中又會遇到各種元素的氧化燒損問題,這種“再氧化”的結果,使不少鋁成為無法再回收的粉態,所謂回收最多也只是含鋁量的30%~50%,回收不了的粉態鋁常被作為“灰渣”鋪路等廢物利用,其余的就完全變化垃圾了。綜上所述,鋁材熔煉過程中損耗的主要去向為:
1、熔煉過程中,各種元素在高溫條件下的氧化燒損;
2、精練過程中,被混在渣中扒出爐外,這種損耗要比前者大好幾倍。
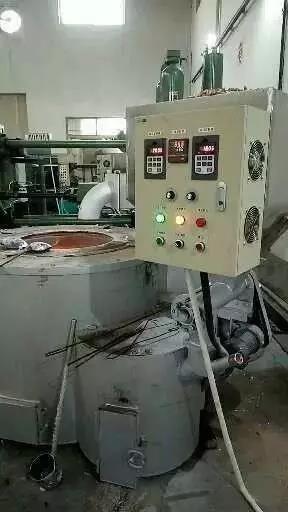
(二)熔煉過程中的氣體及鋁熔渣
1、氣體
在鋁合金熔煉過程中,氣體主要是氫氣,其次是氮氣、氧氣、一氧化碳等。鋁合金中的氫氣主要來源于爐氣中水蒸氣。水蒸氣和鋁液反應生成原子態氫.并在其界面建立起較大的分氣壓,使氫在鋁液中迅速溶解且大量增加,鋁液中的含氫量隨鋁液上的氫分壓和鋁液溫度的升高而增加。
2、氧化夾雜物
夾雜物是指存于液相線溫度以上的任何固相或液相的外生雜質。常見的非金屬夾雜物有氧化物、碳化物、硼化物等,這些夾雜物大都以顆粒或膜狀存在,鋁液和各種氣體反應可以生成氮化鋁、碳化鋁、氧化鋁等。氧化鋁化學穩定性高,在鋁液中不分解。除上述夾雜物之外,鋁熔體中還可能含有熔煉爐和澆包的耐火材料磚、溶劑及其它形式的中間化合物等夾雜物。
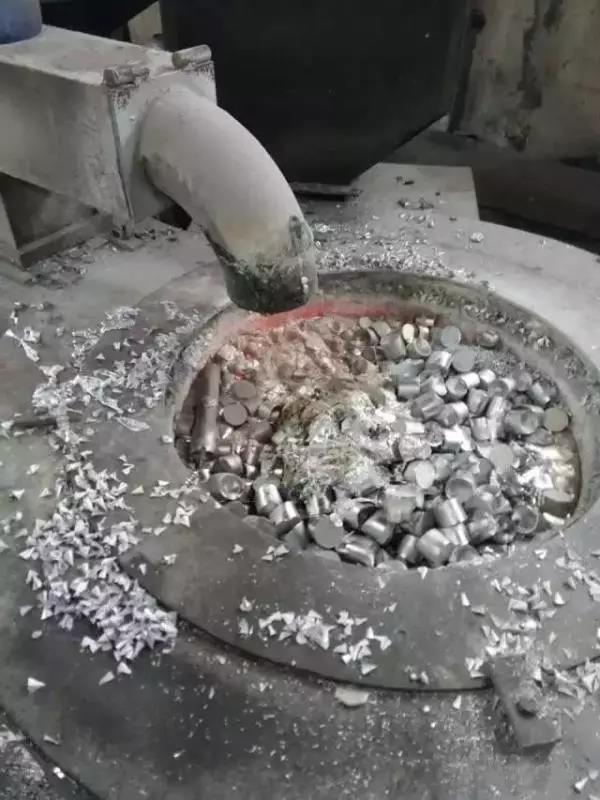
(三)減少熔煉氧化燒損的途徑
1、爐料狀態
經驗證明,爐料在入爐前是否作清潔處理,對氧化渣的產生效果大不一樣,原固是爐料表面的不潔物、油污垢等在高溫狀態下燃燒發熱,溫度急增氧化激烈,形成大量渣滓。因此保持爐料的清潔,對抗燒損是有益的。
2、爐料塊度
應該說,爐料的塊度大小.反映了熔煉過程中,爐料與爐氣中氧接觸的面積大小,從這一點說,爐料塊度越小,意味著與氧接觸面積越大,這對加劇氧化是起促進作用的,尤其是對氧化性氣氛嚴重的反射爐熔煉條件下,應力求不采用過小的爐料塊度。
3、加熱條件
熔池表面爐氣中氧濃度高的熔煉條件,如帶氧助燒噴嘴的熔煉爐,火焰直接與大面積的鋁合金接觸.會激烈加劇爐料的氧化燒損,熔煉溫度和加熱速度對氧化燒損有很大的影響,熔煉溫度過高.對加劇合金氧化有促進作用,加熱速度越快,實際上可縮短熔煉時間,從而減少合金氧化的怍用時間,有利于減少氧化燒損。因此選用熔化效率高的熔煉爐對減少金屬氧化燒損有一定好處。
綜上所述,合金的熔煉加熱條件選擇,實際上是圍繞合金在熔煉過程中如何把握減少與氧在高溫條件下的作用時間的問題,應考慮爐氣氣氛、熔煉溫度和加熱速度的影響因素,合金在熔爐里.尤其是高溫階段.時間越長,越是容易加劇饒損,這在生產管理中是一個很重要的環節,因此合金熔煉結束后,鋁液在爐中長時間停留是十分不利的。
(四)減少精煉過程中的合金損失
4.1 在高溫條件下生成的氧化物與金屬液的浸潤能力雖很差,但鋁液和氧化物仍機械地包混在一起,特別是不干燥的熔劑,更容易產生這種包混現象,通過對添加劑的干燥處理,不僅可以相對降低二者的浸潤作用,且有利于促進添加劑放熱反應,幫助二者分離使鋁液流回熔池,所以熔劑的不干燥,容易帶入氣體.造成更嚴重的氧化饒損
4.2 精煉劑的影響
加精練劑將會分解發熱,進一步加快鋁液的氧化,為了使鋁渣降低浸潤性,促進兩者分離,又不得不加。因此,不僅要選擇好精煉劑種類,同時要控制其適合的加入量。例如用NaC]。比NH4C1的分解溫度低,發熱也小,所以氧化產渣率也小。但加得太多,同樣會增多氧化渣,增加鋁液的損耗
4.3 設法提高渣液分離性能
精煉后浮到液面的渣與金屬液浸潤性很好,兩者緊緊牯附在一起,呈混熔狀態。這時必須加上合適量的“發熱造渣劑”,加入液面后強制燃燒發熱,使液面渣溫升高,使渣中的氧化物和金屬滴浸潤性變差,從而使渣中大的金屬液滴再熔化回到金屬液中,這樣的強制燃燒升溫必然會產生少量的金屬燒損,但比起讓大的鋁液滴被扒出爐外的損失,還是利大于弊,即總損失可大為減少。
綜上所述,降低熔煉損耗的基本出發點可歸納為:
(1)減少熔煉過程中一切促進氧化激烈進行的各種固素,其中包括:
a.嚴格使用經過處理,表面清潔的爐料,金屬錠和壓鑄件毛邊料應存放在干燥的地方并避免與其他物料相混,應該盡量避免室外存放金屬料,以免會增加金屬料被氧化的程度。
b.盡量少用小塊度爐料
c.選擇采用爐氣氛好(氧濃度低)的熔爐和熔鋁條件,制造降低氧濃度的爐氣措施。
d.盡量提高加熱速度,縮短熔煉時間。
(2)嚴格控制精煉過程中的添加劑熔劑種類和加入量。
a.使用惰性氣體精煉法,可減少精煉過程中的氧化燒損
b.用良好的打渣劑促進渣液分離,是使燒損明顯減少的重要關鍵
(3)在溶化金屬錠及毛邊料時,產生一定的氧化是不可避免的,但是在添加金屬料進金屬液池時,也要使金屬液池盡可能受最小的擾動,應當在金屬液池表面保留一層薄的熔渣層,以便減少暴露新鮮金屬液于空氣的機會,只有當熔渣達到1-2cm厚時才除渣。細小的毛削、毛邊及從地面清理而得的廢料有很高的表面積/體積比,潮濕/多油的薄件反工料或機加工的廢料可以進行針對性的方案來確定將細小廢料進行清洗,干燥并擠壓成小塊料,再隨后重熔是否合算。
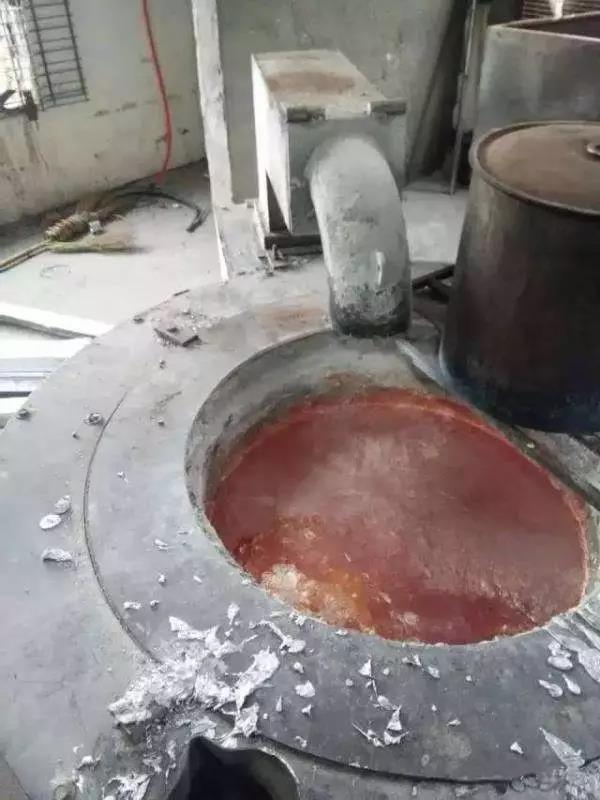
二
熔煉燒損的計算
為了妥善地管理燒損的損失,保持準確的金屬料平衡記錄十分重要。其中包括購買量,生產的鑄件重量,及產生的熔渣量。準確的記錄可以通過比較不同時間內(或許是每月內)地數據,而及時發現任何熔渣數量地變化。除熔煉合金過程損失外,生產過程的損失,產品加工損失,收發貨時重量誤差,不當的庫存記錄,及其它不可預知的因素,在計算公司的整體燒損時,這些額外的損失應扣除掉。
金屬在熔煉過程中由于氧化、精煉、扒渣等原因都會產生損耗。在隨后的鑄造中,鑄件有澆冒口等工藝廢品和廢鑄件需要返回重新熔鑄;鑄坯除了切頭切尾及鑄造廢品需要重新熔鑄外,在加工車間還會有工藝廢料和廢品需要返回鑄造車間重新熔鑄。任何金屬的加工過程中都有一個類似的金屬循環過程,在這一循環過程中,金屬有一定的損耗。顯然,這一循環過程中金屬損耗的多少,與熔煉條件和金屬的性質有關,還與鑄造成品率及加工車間的成品率有關,金屬在一定生產設備和工藝條件下,一定量的金屬原料通過反復循環全部加工成成品,有多少金屬原料被損耗,能生產多少產品?這些問題是每一個生產者和經營者都關心的問題。根據機械工業部JB/T9169.6-1998工藝定額編制標準內的材料消耗工藝定額依據,可參考如下公式對熔煉過程的損耗加以計算:
(1)熔鑄損耗率a a=Ws/W
式中:
WS-熔鑄中損耗的金屬質量(包括氧化與渣中帶走的金屬);
注:熔渣由于可以二次重熔回收及最終處理,因此計算時應考慮回收的價值;
W-投入爐內的金屬總質量。
(2)鑄件成品率b b=Wc/W
式中:Wc-鑄造車間的產品質量
(3)可回收率=回爐料重量/W
(4)不可回收率=(W-Wc-回爐料重量)/W
(5)爐耗率=(W-金屬液重量)/W
(6)金屬液收得率=金屬液重量/W
(7)金屬爐料與焦炭比=W/焦炭重量
根據上述公式,在單純計算熔煉過程中的燒損時,應根據一定時期內投入材料的總重量,減去每次取合金液重量的總合,在減去回收的渣料(熔煉過程的最終渣料價值)才能準確的計算燒損率。
公式7焦炭比在使用天燃氣或其他能源時應加以換算。
上述公司的計算是在設定重量在標準內的,未考慮重量增加的損失。如要計算整個壓鑄過程的材料損失,應對前面所提到的5個相關因素都加以考慮,才能更準確的核算生產過程的材料成本。
三
關于溶渣的處理
采用火焰反射爐熔煉鋁合金,由于爐料不同,渣量為爐料量的2%~5%,而渣中的含鋁量為渣量的40-60%左右。因此,正確的處理鋁爐渣,回收渣中的鋁來降低熔損具有重要的意義,即使采取了所有必要的措施來降低溶渣的產生,含有部分的合金浮渣仍需要定時從熔爐表面上出去。壓鑄車間自行回收可用的壓鑄合金通常需要一個專用的冶煉爐,一攪拌器或其他可用來混合熔煉金屬,以及助溶劑(去渣劑)的裝置。用于生產鑄件的壓鑄機熔爐和蓄料爐一般不適宜處理溶渣,市場上有幾種不同的專利助溶劑,可用來將溶渣分離成可用合金、氧化物和金屬中間相物。如果使用恰當,其中的助溶劑將產生很少甚至不產生煙霧。使用無煙或低煙霧的助溶劑,將會降低廢氣的排放,建議與助溶劑生產廠家直接接洽,以便獲得對該特定產品所適宜的特定工藝。
1.1 扒渣前的處理:精煉后浮到熔體表面的渣,與熔體的浸潤性較好,濕潤角小于90o,渣中混有相當數量的熔體,這一部分熔體呈顆粒狀分散在渣中,與渣粘附在一起。熔體溫度低時兩者的濕潤性更好,若此時扒渣,隨渣帶出的熔體重量約是渣重量的60%。將爐渣量1‰~2‰的造渣劑均勻地撒地熔體表面,來減少渣中的含鋁量。反應物AlF3與鋁、氧發生放熱反應,所釋放的熱量,使粘性熔渣成為松散粉末狀的干性渣。這樣,鋁熔體與渣中氧化物的濕潤性變小,使混在渣中的顆粒狀鋁滴脫離而出,回到熔體中。
1.2 出爐后的鋁渣處理:應當指出,經過上述處理后扒出的渣仍混有鋁滴。在扒渣時,首先將其扒入帶有孔眼的鐵箱內,使一部分粘附在渣上的鋁熔體可滲漏出。扒渣完畢后,再將渣倒入準備好的坑內(經特殊處理),向渣中撒一些造渣劑,同時攪拌,使渣與造渣劑混勻,5~10min后從坑內將渣扒出。依靠造渣劑的快速升溫作用使渣溫達到950℃左右,渣中鋁滴周圍的氧化膜破裂,而鋁滴借助自身重力逐漸匯集落到坑底。經過二次處理的渣就只含有較少量的鋁粒了,將冷卻后的渣存放在一定地方,從中揀選其中的鋁粒。采用上述處理鋁爐渣來回收的方法,簡易可行。目前,在鋁合金熔煉過程中熔損降到1.6%,有時可達到1.4%,如每年生產5000t鋁合金,可將原來因熔損而造成的經濟損失減少40萬元,經濟效益相當可觀。
溶化及生產中金屬液產生溶渣是不可避免的,但是通過恰當的控制、管理溶化和鑄造工藝過程,可以減少溶渣的形成,從而為壓鑄廠商增加較大的利潤。在生產中采用以下所列步驟可以使壓鑄生產中由于溶渣損失而帶來的金屬損耗降低至最小的程度:
(1)購買清潔的、環保的、未被腐蝕的合金錠。將原料存放在清潔、干燥的地方,對于回爐料,也應同樣對待。
(2)通過正確設計及裝配壓鑄模具而降低回爐料的產生量。如此,可以減少或消除毛邊和報廢件的產生。
(3)將潮濕或油瀝的毛邊料或清掃所得的加工廢料處理成干凈、干燥的料塊再重溶。
(4)溶化溫度應盡可能的低而均勻,溶化爐及蓄液爐溫度不應超過750度。
(5)至少應每月一次用手攜式溫度計檢查金屬液的溫度,以確保熔爐溫度計的準確性。
(6)在添加新合金錠或回爐料時,應盡量減少對溶池的攪動。
(7)用多孔的除渣器仔細地除浮渣,并在爐池邊輕抖或拍擊除渣器,以便讓混雜如溶渣中的有用合金液流回池中。
(8)只有必要時才除渣,在溶池表面保留一層浮渣將會減少空氣對金屬液的氧化。
(9)按助溶劑廠家的推薦工藝進行浮渣處理,以確保獲得最大的金屬回收率。
(10)應對溶渣的產生做好詳細的記錄,并定期比較一段時間內產生的溶渣量數據,以便及時發現生產中出現的異常現象。
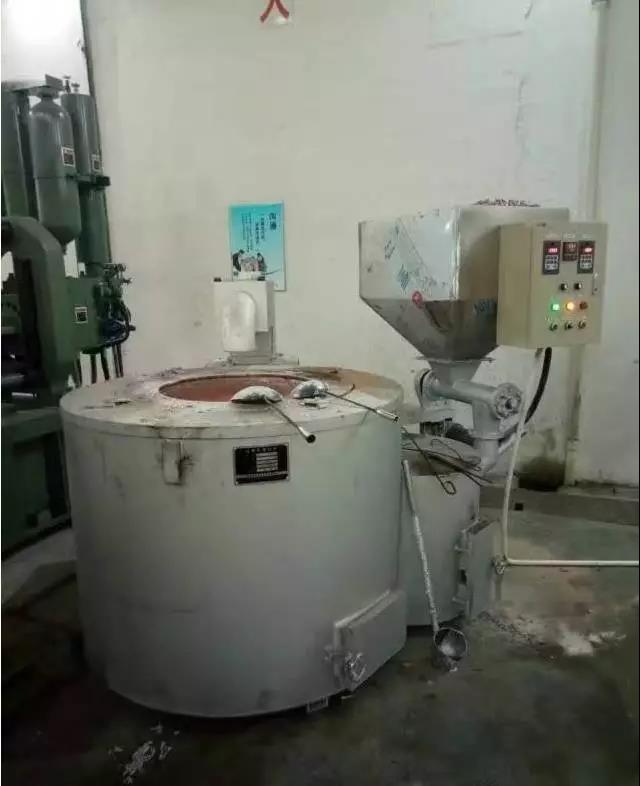
四
鋁及鋁合金熔液的精煉凈化介紹
鋁及鋁合金熔體的精煉凈化方法較多,主要有浮游法、熔劑精煉法、熔體過濾法、真空法和聯合法。本文介紹熔劑精煉法在鋁合金熔煉中的應用。
1、熔劑的作用
鹽熔劑廣泛地用于原鋁和再生鋁的生產,以提高熔體質量和金屬鋁的回收率
熔劑的作用有四個:其一,改變鋁熔體對氧化物(氧化鋁)的潤濕性,使鋁熔體易于與氧化物(氧化鋁)分離,從而使氧化物(氧化鋁)大部分進入熔劑中而減少了熔體中的氧化物的含量。其二,熔劑能改變熔體表面氧化膜的狀態。這是因為它能使熔體表面上那層堅固致密的氧化膜破碎成為細小顆粒,因而有利于熔體中的氫從氧化膜層的顆粒空隙中透過逸出,進入大氣中。其三,熔劑層的存在,能隔絕大氣中水蒸氣與鋁熔體的接觸,使氫難以進入鋁熔體中,同時能防止熔體氧化燒損。其四,熔劑能吸附鋁熔體中的氧化物,使熔體得以凈化。總之,熔劑精煉的除去夾雜物作用主要是通過與熔體中的氧化膜及非金屬夾雜物發生吸附,溶解和化學作用來實現的。
2、熔劑的分類和選擇
2.1熔劑的分類和要求
鋁合金熔煉中使用的熔劑種類很多,可分為覆蓋劑(防止熔體氧化燒損及吸氣的熔劑)和精煉劑(除氣、除夾雜物的熔劑)兩大類,不同的鋁合金所用的覆蓋劑和精煉劑不同。但是,鋁合金熔煉過程中使用的任何熔劑,必須符合下列條件:
①熔點應低于鋁合金的熔化溫度。
②比重應小于鋁合金的比重。
③能吸附、溶解熔體中的夾雜物,并能從熔體中將氣體排除。
④不應與金屬及爐襯起化學作用,如果與金屬起作用時,應只能產生不溶于金屬的惰性氣體,且熔劑應不溶于熔體金屬中。
⑤吸濕性要小,蒸發壓要低。
⑥不應含有或產生有害雜質及氣體。
⑦要有適當的粘度及流動性。
⑧制造方便:價格便宜。
3、鋁合金熔煉中常用熔劑
熔劑精煉法對排出非金屬夾雜物有很好的效果,但是清除熔體中非金屬夾雜物的凈化程度,除與熔劑的物理、化學性能有關外,在很大程度上還取決于精煉工藝條件,如熔劑的用量,熔劑與熔體的接觸時間、接觸面積、攪拌情況、溫度等。為精煉鋁合金熔體,人們已研制出上百種熔劑,以鈉、鉀為基的氯化物熔劑應用最廣。對含鎂量低的鋁合金廣泛采用以鈉鉀為基的氯化物精煉劑,含鎂量高的鋁合金為避免鈉脆性則采用不含鈉的以光鹵石為基的精煉熔劑。
3.3 熔劑使用方法
熔劑精煉法熔煉鋁合金生產中常用以下幾種方法:
①熔體在澆包內精煉。首先在澆包內放入一包熔劑,然后注入熔體,并充分攪拌,以增加二者的接觸面積。
②熔體在感應爐內精煉。熔劑裝入感應爐內,借助于感應磁場的攪拌作用使熔劑與熔體充分混合,達到精煉的目的。
③在澆包內或爐中用攪拌機精煉,使熔劑機械彌散于熔體中。
④熔體在磁場攪拌裝置中精煉。,該法依靠電磁力的作用,向熔劑——金屬界面連續不斷地輸送熔體,以達到鋁熔體與熔劑間的活性接觸,熔體旋轉速度越高,其精煉效果越好。
⑤電熔劑精煉。此法是使熔體通過加有電場(在金屬——熔劑界面上)的熔劑層,進行連續精煉。
總結:
在壓鑄過程中的材料損耗主要為以下幾個方面:
一、熔煉過程的損耗
1、渣料的去除方法,過程還有待改進。
2、各種熔劑的使用是否按要求進行。
3、熔煉過程的溫度是否受控。
4、各種料的配比是否按工藝。
5、除渣、氣過程是否按工藝。
二、各級回爐料的管理
1、在壓鑄過程中廢料、余料的管理不嚴格,浪費較大。
2、回爐料未真正分級,分類管理。
3、回爐料的回收未做好。
三、重量增加、產品生產過程廢品的損失
1、關于重量增加帶來的損失,一方面公司內積極控制,二方面與顧客溝通,重新確認標準重量。
2、減少生產過程的廢品損失。
綜上所述,只有從源頭抓起,各個環節嚴格控制,認真,真實統計過程的數據,才能真正反映公司材料的消耗情況,核算生產成本,更好的利用數據指導經營,降低消耗,提高效益。
壓鑄過程中鋁合金材料損耗有以下幾方面:
1.熔煉中的燒損及揮發;
2.除渣時帶出;
3.壓鑄件飛邊毛刺;
4.澆口、料餅、廢鑄件等重熔的燒損及揮發;
5.因機床、模具等原因,造成壓鑄件重量增加。
一
在溶化金屬過程中的金屬損耗
(一)損耗原因及去向
在鋁合金熔煉過程中,由于鋁氧化以及鋁與爐壁、精煉劑相互作用而造成不可回收的金屬損失叫燒損。燒損和渣中所含的金屬總稱為熔損。只要是大氣條件下作鋁的熔煉,無論是純鋁還是合金,其中的各種元素都要經過高溫條件下的氧化作用,形成各種金屬氧化物,造成鋁液的損耗,自然也就按合金中不同的成分而生成各種不同的氧化物,從而使鋁材受到損耗,熔化完成后的鋁液,還需經過精練,精煉中添加的熔劑又因高溫分解發熱,進一步促使鋁液中各元素的氧化燒損。更使人注目的是,精練完成后,有許多完好的鋁滴,因界面張力的作用被粘附在渣中,成為渣鋁混合物,一起被當作渣扒出爐外。盡管這種混合物還可用很多方法來進行分離回收,但畢竟又需消耗許多能源,且回收過程中又會遇到各種元素的氧化燒損問題,這種“再氧化”的結果,使不少鋁成為無法再回收的粉態,所謂回收最多也只是含鋁量的30%~50%,回收不了的粉態鋁常被作為“灰渣”鋪路等廢物利用,其余的就完全變化垃圾了。綜上所述,鋁材熔煉過程中損耗的主要去向為:
1、熔煉過程中,各種元素在高溫條件下的氧化燒損;
2、精練過程中,被混在渣中扒出爐外,這種損耗要比前者大好幾倍。
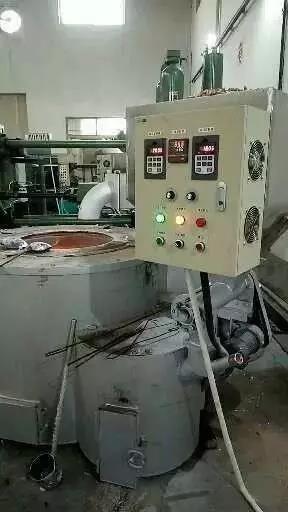
(二)熔煉過程中的氣體及鋁熔渣
1、氣體
在鋁合金熔煉過程中,氣體主要是氫氣,其次是氮氣、氧氣、一氧化碳等。鋁合金中的氫氣主要來源于爐氣中水蒸氣。水蒸氣和鋁液反應生成原子態氫.并在其界面建立起較大的分氣壓,使氫在鋁液中迅速溶解且大量增加,鋁液中的含氫量隨鋁液上的氫分壓和鋁液溫度的升高而增加。
2、氧化夾雜物
夾雜物是指存于液相線溫度以上的任何固相或液相的外生雜質。常見的非金屬夾雜物有氧化物、碳化物、硼化物等,這些夾雜物大都以顆粒或膜狀存在,鋁液和各種氣體反應可以生成氮化鋁、碳化鋁、氧化鋁等。氧化鋁化學穩定性高,在鋁液中不分解。除上述夾雜物之外,鋁熔體中還可能含有熔煉爐和澆包的耐火材料磚、溶劑及其它形式的中間化合物等夾雜物。
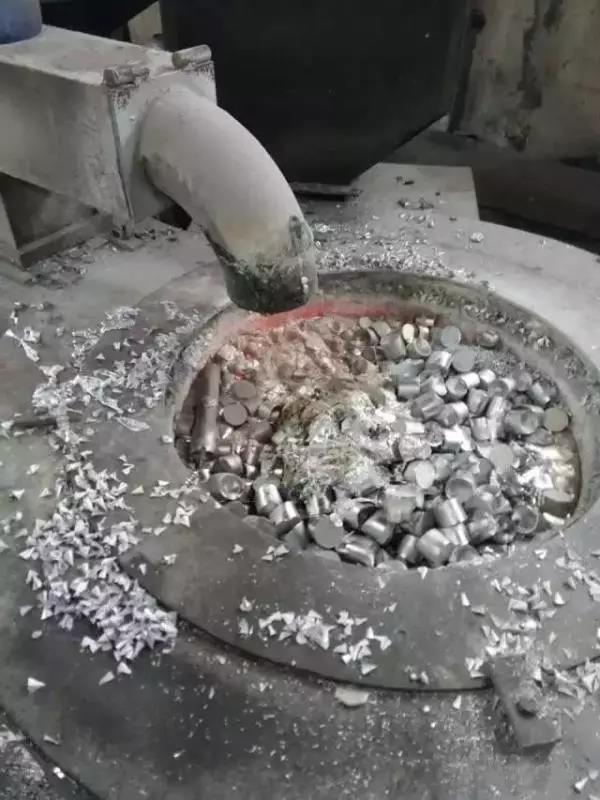
(三)減少熔煉氧化燒損的途徑
1、爐料狀態
經驗證明,爐料在入爐前是否作清潔處理,對氧化渣的產生效果大不一樣,原固是爐料表面的不潔物、油污垢等在高溫狀態下燃燒發熱,溫度急增氧化激烈,形成大量渣滓。因此保持爐料的清潔,對抗燒損是有益的。
2、爐料塊度
應該說,爐料的塊度大小.反映了熔煉過程中,爐料與爐氣中氧接觸的面積大小,從這一點說,爐料塊度越小,意味著與氧接觸面積越大,這對加劇氧化是起促進作用的,尤其是對氧化性氣氛嚴重的反射爐熔煉條件下,應力求不采用過小的爐料塊度。
3、加熱條件
熔池表面爐氣中氧濃度高的熔煉條件,如帶氧助燒噴嘴的熔煉爐,火焰直接與大面積的鋁合金接觸.會激烈加劇爐料的氧化燒損,熔煉溫度和加熱速度對氧化燒損有很大的影響,熔煉溫度過高.對加劇合金氧化有促進作用,加熱速度越快,實際上可縮短熔煉時間,從而減少合金氧化的怍用時間,有利于減少氧化燒損。因此選用熔化效率高的熔煉爐對減少金屬氧化燒損有一定好處。
綜上所述,合金的熔煉加熱條件選擇,實際上是圍繞合金在熔煉過程中如何把握減少與氧在高溫條件下的作用時間的問題,應考慮爐氣氣氛、熔煉溫度和加熱速度的影響因素,合金在熔爐里.尤其是高溫階段.時間越長,越是容易加劇饒損,這在生產管理中是一個很重要的環節,因此合金熔煉結束后,鋁液在爐中長時間停留是十分不利的。
(四)減少精煉過程中的合金損失
4.1 在高溫條件下生成的氧化物與金屬液的浸潤能力雖很差,但鋁液和氧化物仍機械地包混在一起,特別是不干燥的熔劑,更容易產生這種包混現象,通過對添加劑的干燥處理,不僅可以相對降低二者的浸潤作用,且有利于促進添加劑放熱反應,幫助二者分離使鋁液流回熔池,所以熔劑的不干燥,容易帶入氣體.造成更嚴重的氧化饒損
4.2 精煉劑的影響
加精練劑將會分解發熱,進一步加快鋁液的氧化,為了使鋁渣降低浸潤性,促進兩者分離,又不得不加。因此,不僅要選擇好精煉劑種類,同時要控制其適合的加入量。例如用NaC]。比NH4C1的分解溫度低,發熱也小,所以氧化產渣率也小。但加得太多,同樣會增多氧化渣,增加鋁液的損耗
4.3 設法提高渣液分離性能
精煉后浮到液面的渣與金屬液浸潤性很好,兩者緊緊牯附在一起,呈混熔狀態。這時必須加上合適量的“發熱造渣劑”,加入液面后強制燃燒發熱,使液面渣溫升高,使渣中的氧化物和金屬滴浸潤性變差,從而使渣中大的金屬液滴再熔化回到金屬液中,這樣的強制燃燒升溫必然會產生少量的金屬燒損,但比起讓大的鋁液滴被扒出爐外的損失,還是利大于弊,即總損失可大為減少。
綜上所述,降低熔煉損耗的基本出發點可歸納為:
(1)減少熔煉過程中一切促進氧化激烈進行的各種固素,其中包括:
a.嚴格使用經過處理,表面清潔的爐料,金屬錠和壓鑄件毛邊料應存放在干燥的地方并避免與其他物料相混,應該盡量避免室外存放金屬料,以免會增加金屬料被氧化的程度。
b.盡量少用小塊度爐料
c.選擇采用爐氣氛好(氧濃度低)的熔爐和熔鋁條件,制造降低氧濃度的爐氣措施。
d.盡量提高加熱速度,縮短熔煉時間。
(2)嚴格控制精煉過程中的添加劑熔劑種類和加入量。
a.使用惰性氣體精煉法,可減少精煉過程中的氧化燒損
b.用良好的打渣劑促進渣液分離,是使燒損明顯減少的重要關鍵
(3)在溶化金屬錠及毛邊料時,產生一定的氧化是不可避免的,但是在添加金屬料進金屬液池時,也要使金屬液池盡可能受最小的擾動,應當在金屬液池表面保留一層薄的熔渣層,以便減少暴露新鮮金屬液于空氣的機會,只有當熔渣達到1-2cm厚時才除渣。細小的毛削、毛邊及從地面清理而得的廢料有很高的表面積/體積比,潮濕/多油的薄件反工料或機加工的廢料可以進行針對性的方案來確定將細小廢料進行清洗,干燥并擠壓成小塊料,再隨后重熔是否合算。
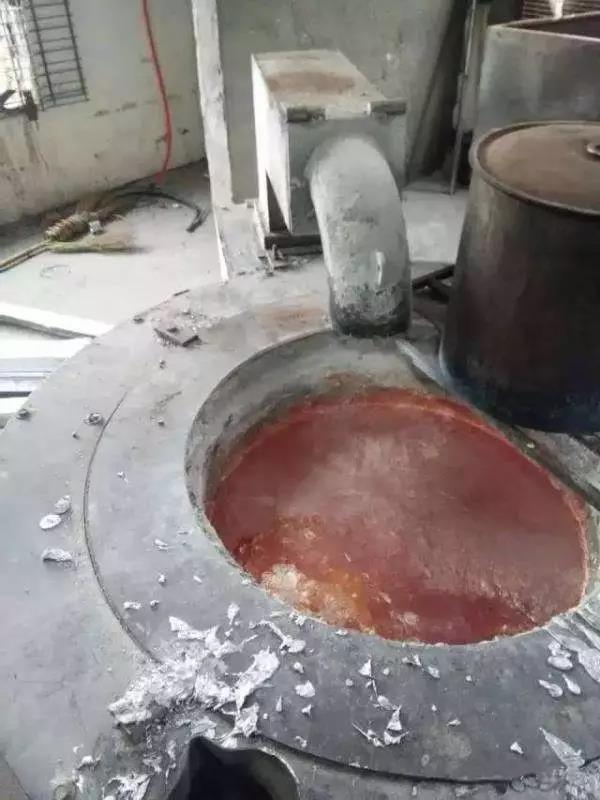
二
熔煉燒損的計算
為了妥善地管理燒損的損失,保持準確的金屬料平衡記錄十分重要。其中包括購買量,生產的鑄件重量,及產生的熔渣量。準確的記錄可以通過比較不同時間內(或許是每月內)地數據,而及時發現任何熔渣數量地變化。除熔煉合金過程損失外,生產過程的損失,產品加工損失,收發貨時重量誤差,不當的庫存記錄,及其它不可預知的因素,在計算公司的整體燒損時,這些額外的損失應扣除掉。
金屬在熔煉過程中由于氧化、精煉、扒渣等原因都會產生損耗。在隨后的鑄造中,鑄件有澆冒口等工藝廢品和廢鑄件需要返回重新熔鑄;鑄坯除了切頭切尾及鑄造廢品需要重新熔鑄外,在加工車間還會有工藝廢料和廢品需要返回鑄造車間重新熔鑄。任何金屬的加工過程中都有一個類似的金屬循環過程,在這一循環過程中,金屬有一定的損耗。顯然,這一循環過程中金屬損耗的多少,與熔煉條件和金屬的性質有關,還與鑄造成品率及加工車間的成品率有關,金屬在一定生產設備和工藝條件下,一定量的金屬原料通過反復循環全部加工成成品,有多少金屬原料被損耗,能生產多少產品?這些問題是每一個生產者和經營者都關心的問題。根據機械工業部JB/T9169.6-1998工藝定額編制標準內的材料消耗工藝定額依據,可參考如下公式對熔煉過程的損耗加以計算:
(1)熔鑄損耗率a a=Ws/W
式中:
WS-熔鑄中損耗的金屬質量(包括氧化與渣中帶走的金屬);
注:熔渣由于可以二次重熔回收及最終處理,因此計算時應考慮回收的價值;
W-投入爐內的金屬總質量。
(2)鑄件成品率b b=Wc/W
式中:Wc-鑄造車間的產品質量
(3)可回收率=回爐料重量/W
(4)不可回收率=(W-Wc-回爐料重量)/W
(5)爐耗率=(W-金屬液重量)/W
(6)金屬液收得率=金屬液重量/W
(7)金屬爐料與焦炭比=W/焦炭重量
根據上述公式,在單純計算熔煉過程中的燒損時,應根據一定時期內投入材料的總重量,減去每次取合金液重量的總合,在減去回收的渣料(熔煉過程的最終渣料價值)才能準確的計算燒損率。
公式7焦炭比在使用天燃氣或其他能源時應加以換算。
上述公司的計算是在設定重量在標準內的,未考慮重量增加的損失。如要計算整個壓鑄過程的材料損失,應對前面所提到的5個相關因素都加以考慮,才能更準確的核算生產過程的材料成本。
三
關于溶渣的處理
采用火焰反射爐熔煉鋁合金,由于爐料不同,渣量為爐料量的2%~5%,而渣中的含鋁量為渣量的40-60%左右。因此,正確的處理鋁爐渣,回收渣中的鋁來降低熔損具有重要的意義,即使采取了所有必要的措施來降低溶渣的產生,含有部分的合金浮渣仍需要定時從熔爐表面上出去。壓鑄車間自行回收可用的壓鑄合金通常需要一個專用的冶煉爐,一攪拌器或其他可用來混合熔煉金屬,以及助溶劑(去渣劑)的裝置。用于生產鑄件的壓鑄機熔爐和蓄料爐一般不適宜處理溶渣,市場上有幾種不同的專利助溶劑,可用來將溶渣分離成可用合金、氧化物和金屬中間相物。如果使用恰當,其中的助溶劑將產生很少甚至不產生煙霧。使用無煙或低煙霧的助溶劑,將會降低廢氣的排放,建議與助溶劑生產廠家直接接洽,以便獲得對該特定產品所適宜的特定工藝。
1.1 扒渣前的處理:精煉后浮到熔體表面的渣,與熔體的浸潤性較好,濕潤角小于90o,渣中混有相當數量的熔體,這一部分熔體呈顆粒狀分散在渣中,與渣粘附在一起。熔體溫度低時兩者的濕潤性更好,若此時扒渣,隨渣帶出的熔體重量約是渣重量的60%。將爐渣量1‰~2‰的造渣劑均勻地撒地熔體表面,來減少渣中的含鋁量。反應物AlF3與鋁、氧發生放熱反應,所釋放的熱量,使粘性熔渣成為松散粉末狀的干性渣。這樣,鋁熔體與渣中氧化物的濕潤性變小,使混在渣中的顆粒狀鋁滴脫離而出,回到熔體中。
1.2 出爐后的鋁渣處理:應當指出,經過上述處理后扒出的渣仍混有鋁滴。在扒渣時,首先將其扒入帶有孔眼的鐵箱內,使一部分粘附在渣上的鋁熔體可滲漏出。扒渣完畢后,再將渣倒入準備好的坑內(經特殊處理),向渣中撒一些造渣劑,同時攪拌,使渣與造渣劑混勻,5~10min后從坑內將渣扒出。依靠造渣劑的快速升溫作用使渣溫達到950℃左右,渣中鋁滴周圍的氧化膜破裂,而鋁滴借助自身重力逐漸匯集落到坑底。經過二次處理的渣就只含有較少量的鋁粒了,將冷卻后的渣存放在一定地方,從中揀選其中的鋁粒。采用上述處理鋁爐渣來回收的方法,簡易可行。目前,在鋁合金熔煉過程中熔損降到1.6%,有時可達到1.4%,如每年生產5000t鋁合金,可將原來因熔損而造成的經濟損失減少40萬元,經濟效益相當可觀。
溶化及生產中金屬液產生溶渣是不可避免的,但是通過恰當的控制、管理溶化和鑄造工藝過程,可以減少溶渣的形成,從而為壓鑄廠商增加較大的利潤。在生產中采用以下所列步驟可以使壓鑄生產中由于溶渣損失而帶來的金屬損耗降低至最小的程度:
(1)購買清潔的、環保的、未被腐蝕的合金錠。將原料存放在清潔、干燥的地方,對于回爐料,也應同樣對待。
(2)通過正確設計及裝配壓鑄模具而降低回爐料的產生量。如此,可以減少或消除毛邊和報廢件的產生。
(3)將潮濕或油瀝的毛邊料或清掃所得的加工廢料處理成干凈、干燥的料塊再重溶。
(4)溶化溫度應盡可能的低而均勻,溶化爐及蓄液爐溫度不應超過750度。
(5)至少應每月一次用手攜式溫度計檢查金屬液的溫度,以確保熔爐溫度計的準確性。
(6)在添加新合金錠或回爐料時,應盡量減少對溶池的攪動。
(7)用多孔的除渣器仔細地除浮渣,并在爐池邊輕抖或拍擊除渣器,以便讓混雜如溶渣中的有用合金液流回池中。
(8)只有必要時才除渣,在溶池表面保留一層浮渣將會減少空氣對金屬液的氧化。
(9)按助溶劑廠家的推薦工藝進行浮渣處理,以確保獲得最大的金屬回收率。
(10)應對溶渣的產生做好詳細的記錄,并定期比較一段時間內產生的溶渣量數據,以便及時發現生產中出現的異常現象。
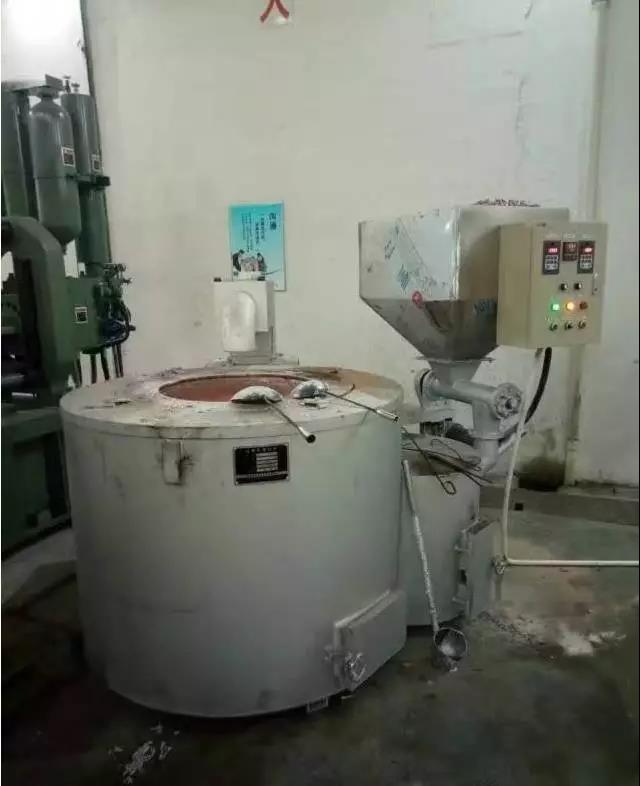
四
鋁及鋁合金熔液的精煉凈化介紹
鋁及鋁合金熔體的精煉凈化方法較多,主要有浮游法、熔劑精煉法、熔體過濾法、真空法和聯合法。本文介紹熔劑精煉法在鋁合金熔煉中的應用。
1、熔劑的作用
鹽熔劑廣泛地用于原鋁和再生鋁的生產,以提高熔體質量和金屬鋁的回收率
熔劑的作用有四個:其一,改變鋁熔體對氧化物(氧化鋁)的潤濕性,使鋁熔體易于與氧化物(氧化鋁)分離,從而使氧化物(氧化鋁)大部分進入熔劑中而減少了熔體中的氧化物的含量。其二,熔劑能改變熔體表面氧化膜的狀態。這是因為它能使熔體表面上那層堅固致密的氧化膜破碎成為細小顆粒,因而有利于熔體中的氫從氧化膜層的顆粒空隙中透過逸出,進入大氣中。其三,熔劑層的存在,能隔絕大氣中水蒸氣與鋁熔體的接觸,使氫難以進入鋁熔體中,同時能防止熔體氧化燒損。其四,熔劑能吸附鋁熔體中的氧化物,使熔體得以凈化。總之,熔劑精煉的除去夾雜物作用主要是通過與熔體中的氧化膜及非金屬夾雜物發生吸附,溶解和化學作用來實現的。
2、熔劑的分類和選擇
2.1熔劑的分類和要求
鋁合金熔煉中使用的熔劑種類很多,可分為覆蓋劑(防止熔體氧化燒損及吸氣的熔劑)和精煉劑(除氣、除夾雜物的熔劑)兩大類,不同的鋁合金所用的覆蓋劑和精煉劑不同。但是,鋁合金熔煉過程中使用的任何熔劑,必須符合下列條件:
①熔點應低于鋁合金的熔化溫度。
②比重應小于鋁合金的比重。
③能吸附、溶解熔體中的夾雜物,并能從熔體中將氣體排除。
④不應與金屬及爐襯起化學作用,如果與金屬起作用時,應只能產生不溶于金屬的惰性氣體,且熔劑應不溶于熔體金屬中。
⑤吸濕性要小,蒸發壓要低。
⑥不應含有或產生有害雜質及氣體。
⑦要有適當的粘度及流動性。
⑧制造方便:價格便宜。
3、鋁合金熔煉中常用熔劑
熔劑精煉法對排出非金屬夾雜物有很好的效果,但是清除熔體中非金屬夾雜物的凈化程度,除與熔劑的物理、化學性能有關外,在很大程度上還取決于精煉工藝條件,如熔劑的用量,熔劑與熔體的接觸時間、接觸面積、攪拌情況、溫度等。為精煉鋁合金熔體,人們已研制出上百種熔劑,以鈉、鉀為基的氯化物熔劑應用最廣。對含鎂量低的鋁合金廣泛采用以鈉鉀為基的氯化物精煉劑,含鎂量高的鋁合金為避免鈉脆性則采用不含鈉的以光鹵石為基的精煉熔劑。
3.3 熔劑使用方法
熔劑精煉法熔煉鋁合金生產中常用以下幾種方法:
①熔體在澆包內精煉。首先在澆包內放入一包熔劑,然后注入熔體,并充分攪拌,以增加二者的接觸面積。
②熔體在感應爐內精煉。熔劑裝入感應爐內,借助于感應磁場的攪拌作用使熔劑與熔體充分混合,達到精煉的目的。
③在澆包內或爐中用攪拌機精煉,使熔劑機械彌散于熔體中。
④熔體在磁場攪拌裝置中精煉。,該法依靠電磁力的作用,向熔劑——金屬界面連續不斷地輸送熔體,以達到鋁熔體與熔劑間的活性接觸,熔體旋轉速度越高,其精煉效果越好。
⑤電熔劑精煉。此法是使熔體通過加有電場(在金屬——熔劑界面上)的熔劑層,進行連續精煉。
總結:
在壓鑄過程中的材料損耗主要為以下幾個方面:
一、熔煉過程的損耗
1、渣料的去除方法,過程還有待改進。
2、各種熔劑的使用是否按要求進行。
3、熔煉過程的溫度是否受控。
4、各種料的配比是否按工藝。
5、除渣、氣過程是否按工藝。
二、各級回爐料的管理
1、在壓鑄過程中廢料、余料的管理不嚴格,浪費較大。
2、回爐料未真正分級,分類管理。
3、回爐料的回收未做好。
三、重量增加、產品生產過程廢品的損失
1、關于重量增加帶來的損失,一方面公司內積極控制,二方面與顧客溝通,重新確認標準重量。
2、減少生產過程的廢品損失。
綜上所述,只有從源頭抓起,各個環節嚴格控制,認真,真實統計過程的數據,才能真正反映公司材料的消耗情況,核算生產成本,更好的利用數據指導經營,降低消耗,提高效益。
相關文章